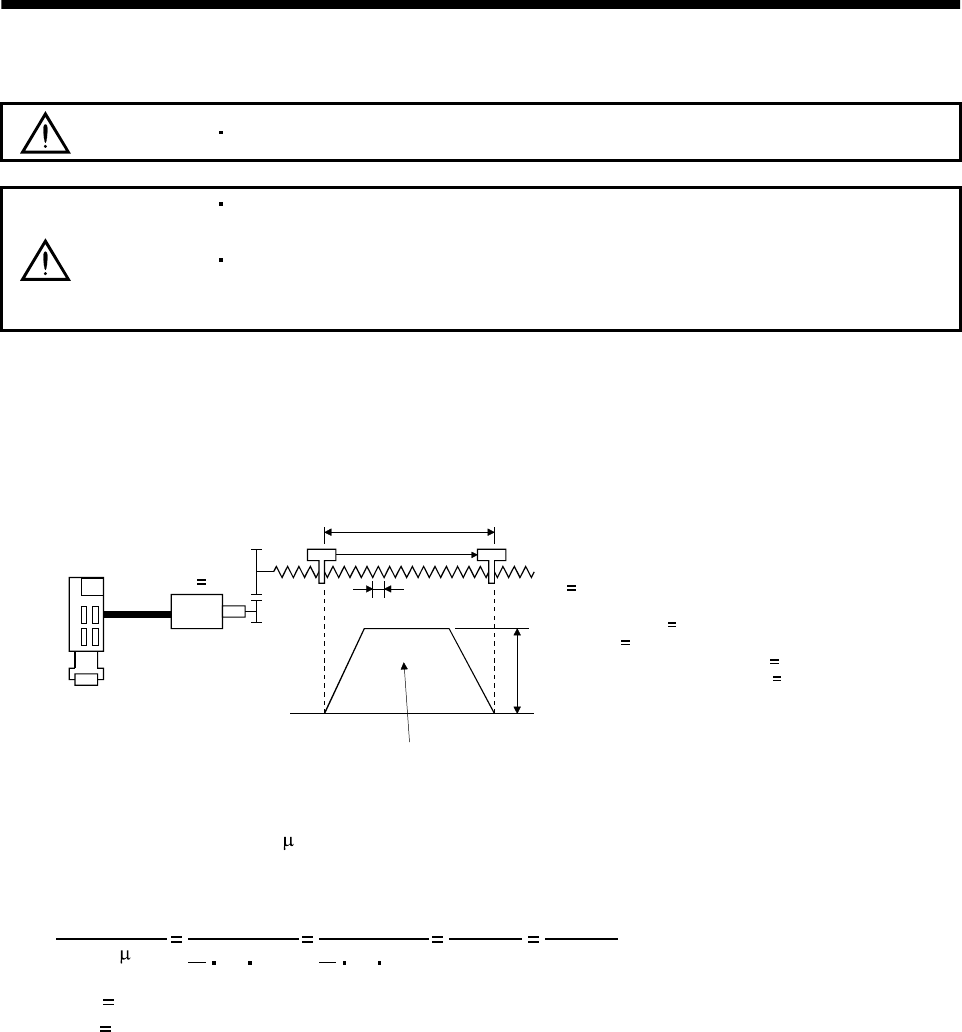
4 - 2
4. OPERATION
4.1.2 Startup
WARNING
Do not operate the switches with wet hands. You may get an electric shock.
CAUTION
Before starting operation, check the parameters. Some machines may perform
unexpected operation.
During power-on or soon after power-off, do not touch the servo amplifier heat
sink, regenerative brake resistor, servo motor, etc. as they may be at high
temperatures. You may get burnt.
Connect the servo motor with a machine after confirming that the servo motor operates properly alone.
For startup reference, a single machine structure will be described. Refer to this section and start up the
machine safely.
(1) Machine conditions
Program No. 2
Servo motor
HC-MFS131072pulse/rev
Servo motor
speed
Ballscrew
P
B
10mm(0.39inch)
Reduction ratio
1/n 1/2
Servo amplifier
Regenerative
brake option
MR-RB032
Ta
Tb
0r/min
V
Position data (P) 200mm(787.40inch)
Speed (V) 2500r/min
Acceleration time constant (Ta) 200ms
Deceleration time constant (Tb) 300ms
P
P
B
1) Absolute position detection system used
2) Command resolution: 10
m
3) Command system: Absolute value command system
4) Electronic gear calculation
CMX(pulse)
CDV( m)
131072 131072
10
131072
5000
32768
1250
1
n
P
B
1000
1000
1
2
........................................................(4.1)
CMX 32768
CDV
1250
5) External input signals are used by the program selection, forward rotation start (ST1), servo-on
(SON) and other commands.
6) Program No.2 is used to execute program operation once.