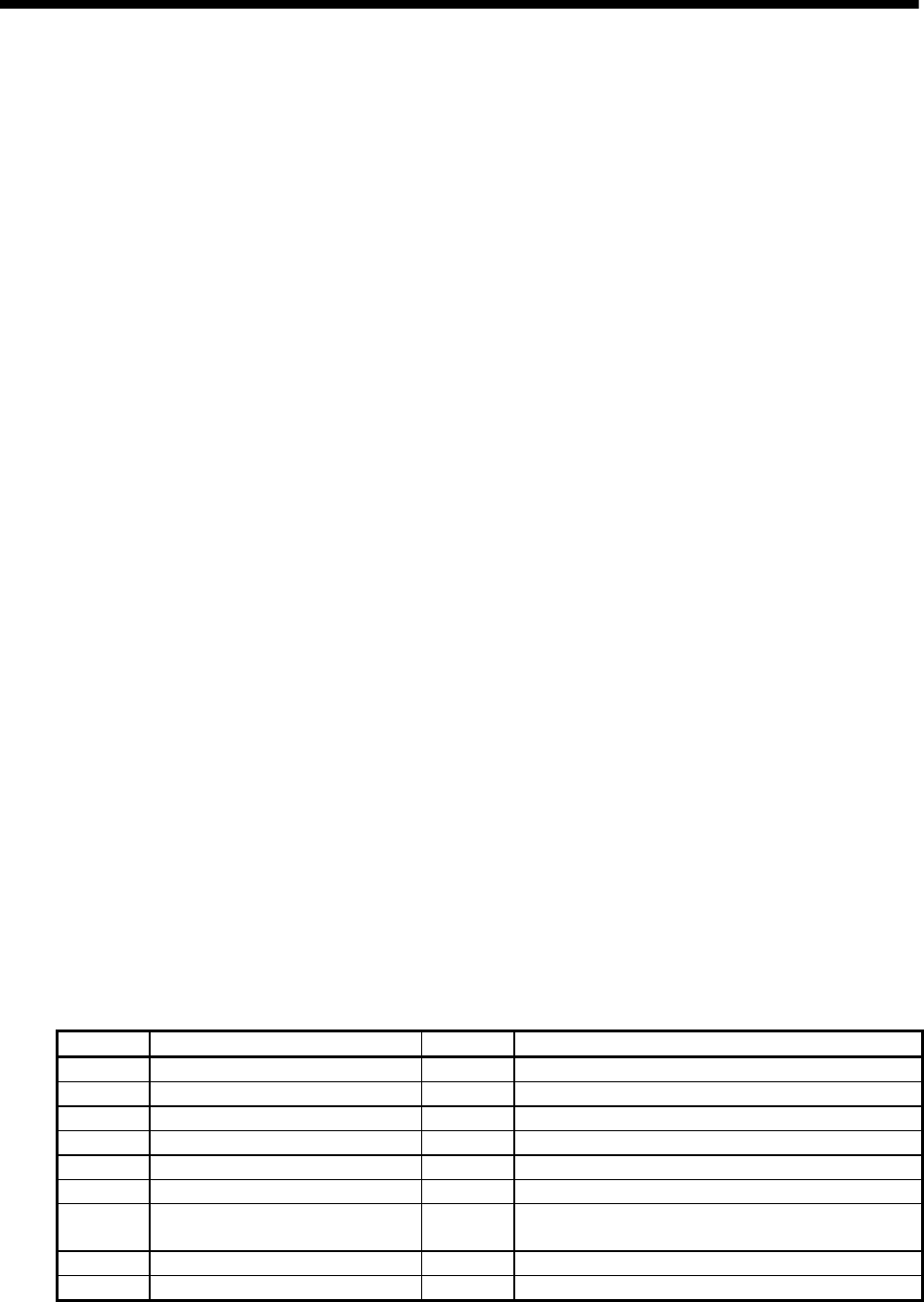
4 - 5
4. OPERATION
(6) Stop
In any of the following statuses, the servo amplifier interrupts and stops the operation of the servo
motor:
Refer to Section 3.8, (2) for the servo motor equipped with electromagnetic brake. Note that
simultaneous ON or simultaneous OFF of stroke end (LSP, LSN) OFF and forward rotation start (ST1)
or reverse rotation start (ST2) signal has the same stop pattern as described below.
(a) Servo on (SON) OFF
The base circuit is shut off and the servo motor coasts.
(b) Alarm occurrence
When an alarm occurs, the base circuit is shut off and the dynamic brake is operated to bring the
servo motor to a sudden stop.
(c) Forced stop (EMG) OFF
The base circuit is shut off and the dynamic brake is operated to bring the servo motor to a sudden
stop. Alarm A. E6 occurs.
(d) Stroke end (LSP/LSN) OFF
The servo motor is brought to a sudden stop and servo-locked. The motor may be run in the opposite
direction.
(e) Simultaneous ON or simultaneous OFF of forward rotation start (ST1) and reverse rotation start
(ST2) signals
The servo motor is decelerated to a stop.
4.2.4 Torque control mode
(1) Power on
(a) Switch off the servo on (SON) signal.
(b) When main circuit power/control circuit power is switched on, "U (torque command voltage)"
appears on the parameter unit.
(2) Test operation
Using jog operation in the "test operation mode" of the Parameter unit, make sure that the servo motor
operates. (Refer to Section 6.8.2.)
(3) Parameter setting
Set the parameters according to the structure and specifications of the machine. Refer to Chapter 5 for
the parameter definitions and to Sections 6.5 for the setting method.
Parameter Name Setting Description
No. 0 Select the control mode 4 First digit : Torque control mode
No. 8 Internal speed command 1 1000 Set 1000r/min.
No. 9 Internal speed command 2 1500 Set 1500r/min.
No. 10 Internal speed command 3 2000 Set 2000r/min.
No. 11 Acceleration time constant 1000 Set 1000ms.
No. 12 Deceleration time constant 500 Set 500ms.
No. 13
S-pattern acceleration/deceleration
time constant
0 Not used
No. 14 Torque command time constant 2000 Set 2000ms
No. 28 Internal torque limit 1 50 Controlled to 50% output
After setting the above parameters, switch power off once. Then switch power on again to make the
set parameter values valid.