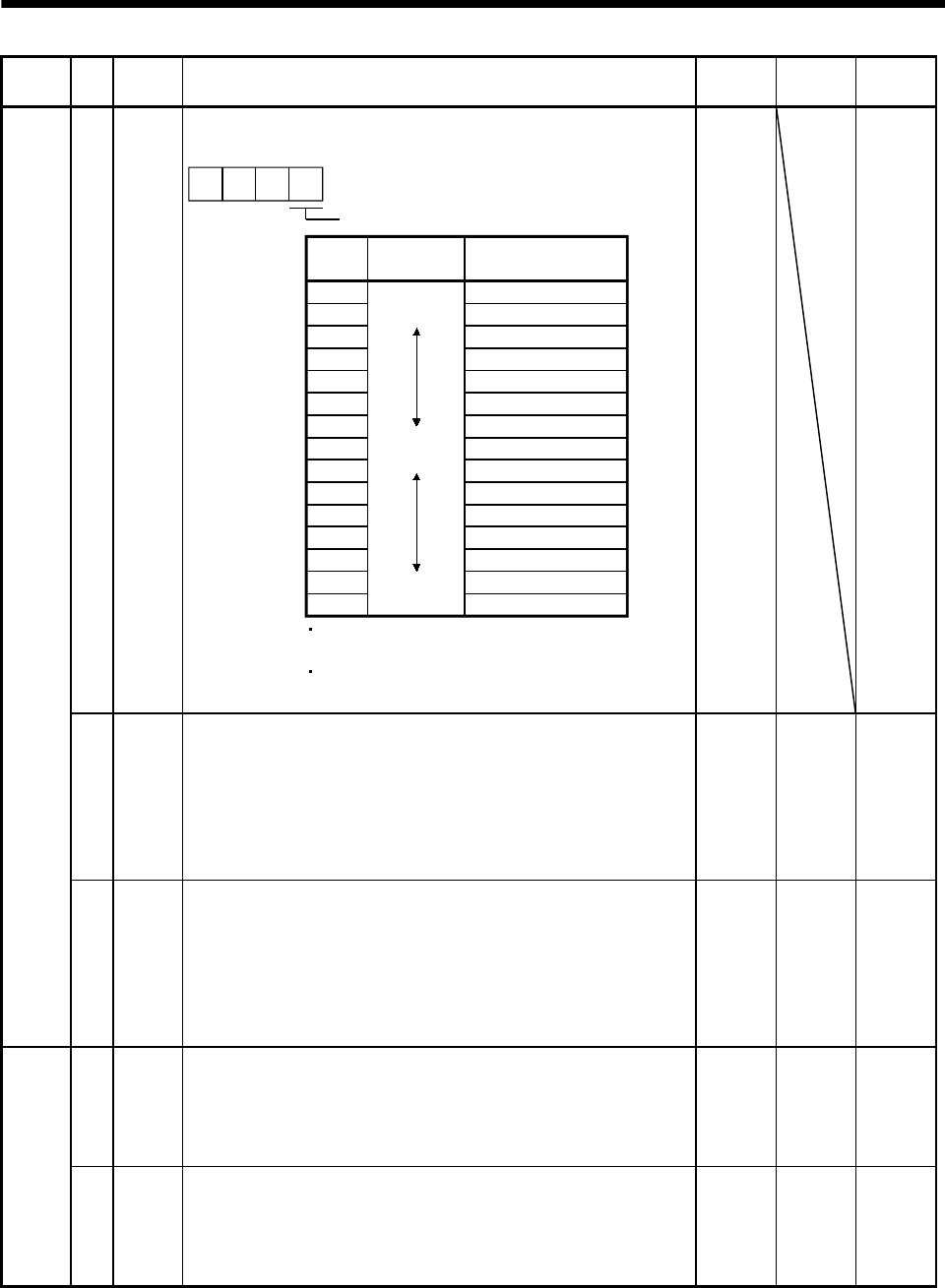
5 - 6
5. PARAMETERS
Classifi-
cation
No. Symbol Name and Function
Initial
Value
Unit
Setting
Range
9 RSP Servo response
Used to select the response of auto tuning.
Response level selection
If the machine hunts or generates large gear
sound, decrease the set value.
To improve performance, e.g. shorten the
settling time, increase the set value.
Set
value
Response
level
1
Low
response
Middle
response
High
response
Machine resonance
frequency guideline
15Hz
2
20Hz
3
25Hz
4
30Hz
5
35Hz
6
45Hz
7
55Hz
8
70Hz
9
85Hz
A
105Hz
B
130Hz
C
160Hz
D
200Hz
E
240Hz
F300Hz
0 00
7kW or
less
:0005
11kW or
more
:0002
Refer to
name
and
function
column.
10 TLP Forward rotation torque limit
Assume that the rated torque is 100[%].
Used to limit the torque in the forward rotation driving mode and
reverse rotation regenerative mode.
In other than the test operation mode on the MR Configurator (servo
configuration software), the torque limit value on the servo system
controller side is made valid.
300 % 0
to
500
Basic parameters
11 TLN Reverse rotation torque limit
Assume that the rated torque is 100[%].
Used to limit the torque in the forward rotation driving mode and
forward rotation regenerative mode.
In other than the test operation mode on the MR Configurator (servo
configuration software), the torque limit value on the servo system
controller side is made valid.
300 % 0
to
500
12 GD2 Ratio of load inertia to servo motor inertia (load inertia ratio)
Used to set the ratio of the load inertia (inertia moment) to the
inertia moment of the servo motor shaft. When auto tuning mode 1
and interpolation mode is selected, the result of auto tuning is
automatically used. (Refer to section 6.1.1)
7.0 times 0.0
to
300.0
Adjustment parameters
13 PG1 Position control gain 1
Used to set the gain of position loop 1. Increase the gain to improve
track ability performance in response to the position command.
When auto turning mode 1,2 is selected, the result of auto turning is
automatically used.
7kW or
less:35
11kW or
more:19
rad/s 4
to
2000