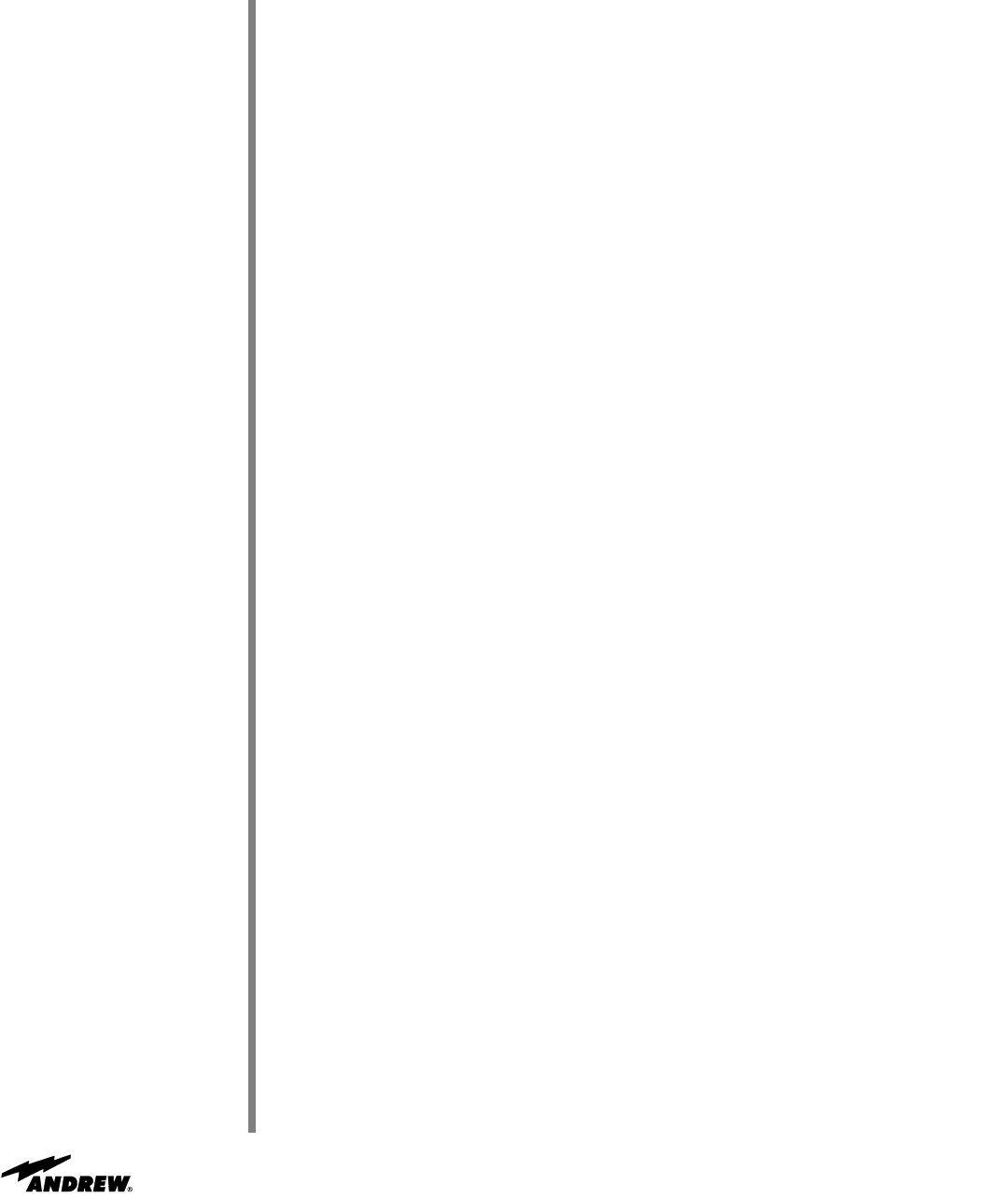
Jackscrews/Motors
Gear
Motor/Housing Fill
Drain
Requirements
80
the application of lubricant to any parts, use a clean cloth and/or bristle brush and
remove any old lubricant to prevent an excessive build-up. Remove indicated access
plugs from square tube weldment and apply lubricant to panning frame tube assembly
and corresponding thrust pads. Securely replace access plugs in square tube weldment.
Be certain to remove any protective caps and clean off each lubrication fitting prior to
injecting fresh grease. The elevation and azimuth jackscrew assemblies are equipped
with a grease fitting and corresponding pipe plug on opposite sides of the jack housing.
Remove the appropriate pipe plug and fill it with grease until lubricant seeps from pipe
plug opening. Replace and securely tighten pipe plug.
The following is a list of the lubricant characteristics:
• Mobil Temp SHC32 A non-soap hydrocarbon fluid type grease. Operating tempera-
ture is -65 degrees to 350+ degrees Fahrenheit (-54 degrees to
177+ degrees Celsius).
• Mobil SHC624 A low temperature synthetic oil for worm gear reducers.
Operating temperature range is -40 degrees to 125+ degrees
Fahrenheit (-40 degrees to 52+ degrees Celsius).
• Moly Grease A grease lubricant containing molybdenum disulfide. Operating
Lubricant temperature range is -85 degrees to 300+ degrees
Fahrenheit (-29 degrees to 149+ degrees Celsius).
Periodically inspect lifting screws on jackscrew assemblies to insure adequate lubrica-
tion. Loosen jackscrew boot clamps to expose the lifting screw assembly. Fully extend
jackscrew assembly, being careful not to exceed preset mechanical limits. Brush thin
coating of Mobil SHC32 grease on exposed lifting screw. Replace boot and attach corre-
sponding boot clamps. If lifting screw is rusty, remove existing lubricant with solvent and
wire brush rusted area. Rinse with solvent and apply fresh grease.
Periodically inspect and remove dust and dirt deposits from the motor housings to avoid
hindering the thread exchange with the ambient air. Slight dirt accumulation on the air
vent screw through splash oil cannot be avoided, however, keep vent screw clean to
ensure proper pressure compensation.
Lube points 2 and 4, shown in Table 1, require removal of the indicated drain plugs and
collecting/measuring the amount of SHC624 drain oil using measuring cup. The speci-
fied amount of oil must be added to the gear motor/hosing (after installing the drain
plug) via the fill/vent plug opening using supplied funnel. Addition of the oil requires use
of an appropriate filling utensil. Use of a modified level stick will not correctly gauge the
appropriate amount of oil in the gear housings.
Preventive Maintenance