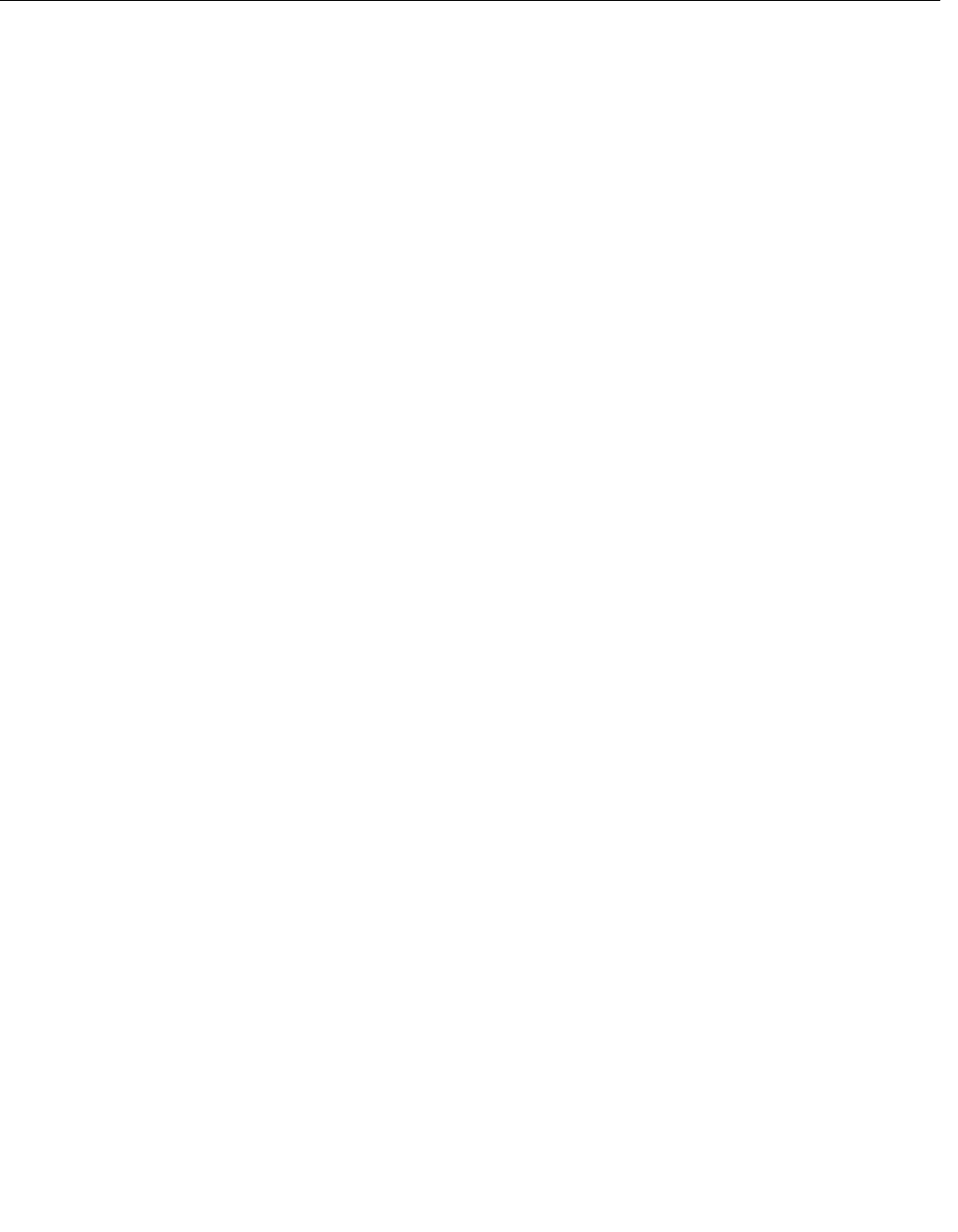
Reference Manual
00809-0100-4696, Rev AA
September 2004
E-3
Rosemount 848L
Restart Delay
A motor may be used in a condition where starting is difficult, causing the
motor to heat rapidly until it gets running. That heat must be allowed to
dissipate before the motor is started again. A simple time delay prevents the
start button from working until a fixed delay time expires. Another example is
the time required for compressor head pressure to bleed off after the
compressor motor stops.
Maximum Restarts
Another way of handling difficult starts is to count the number of starts in a
given time and lock out the start button if the count is exceeded. Locking it out
means that the start button will not function until a latching relay has been
manually reset by an operator who has verified the safety of the situation.
Winding temperature
The above restart limiters may not be necessary if the winding temperature
can be measured and used as a permissive for starting. The winding
temperature sensor may be a ten ohm length of copper wire that is wound into
the motor along with the power windings.
Hand-Off-Auto
An operator may be required to perform some function near the motor, such
as clean a pump strainer or jog the motor to get its load into the right position.
The motor is normally controlled by the central system but must have a local
station to allow the local operator to control the motor. The local station has
buttons for Stop and Start, and a three position switch for Hand-Off-Auto
(HOA) selection. The control room has control when the switch is in the Auto
position. The motor will not run when the switch is in the Off position. The
Hand position allows the local start and stop buttons to control the motor. The
Off position is not as secure as the lockout procedure required when the
equipment or the operator would be damaged if the motor started. This
requires all concerned people to physically put a padlock on the Off position of
the main circuit breaker for the motor. The motor may be started after the last
person removes their lock.
Intermediate Stop
A reversible motor may be required to come to a complete stop before starting
to run in the other direction. This may be done with a timer or a motion sensor
on the motor (or driven load) shaft.
Redundant Motors
The process may require redundant motors for reliability. Usually this applies
to pumps, so that there is no mechanical connection between the two motors.
One pump may be shut off to replace seals (or the entire pump and motor)
while the redundant pump maintains flow in the line. There are three ways to
control redundant pumps:
Alternate Start
When the start button is pressed the pump that was not in use is started. Not
in use refers to now or since the last time start was pressed.