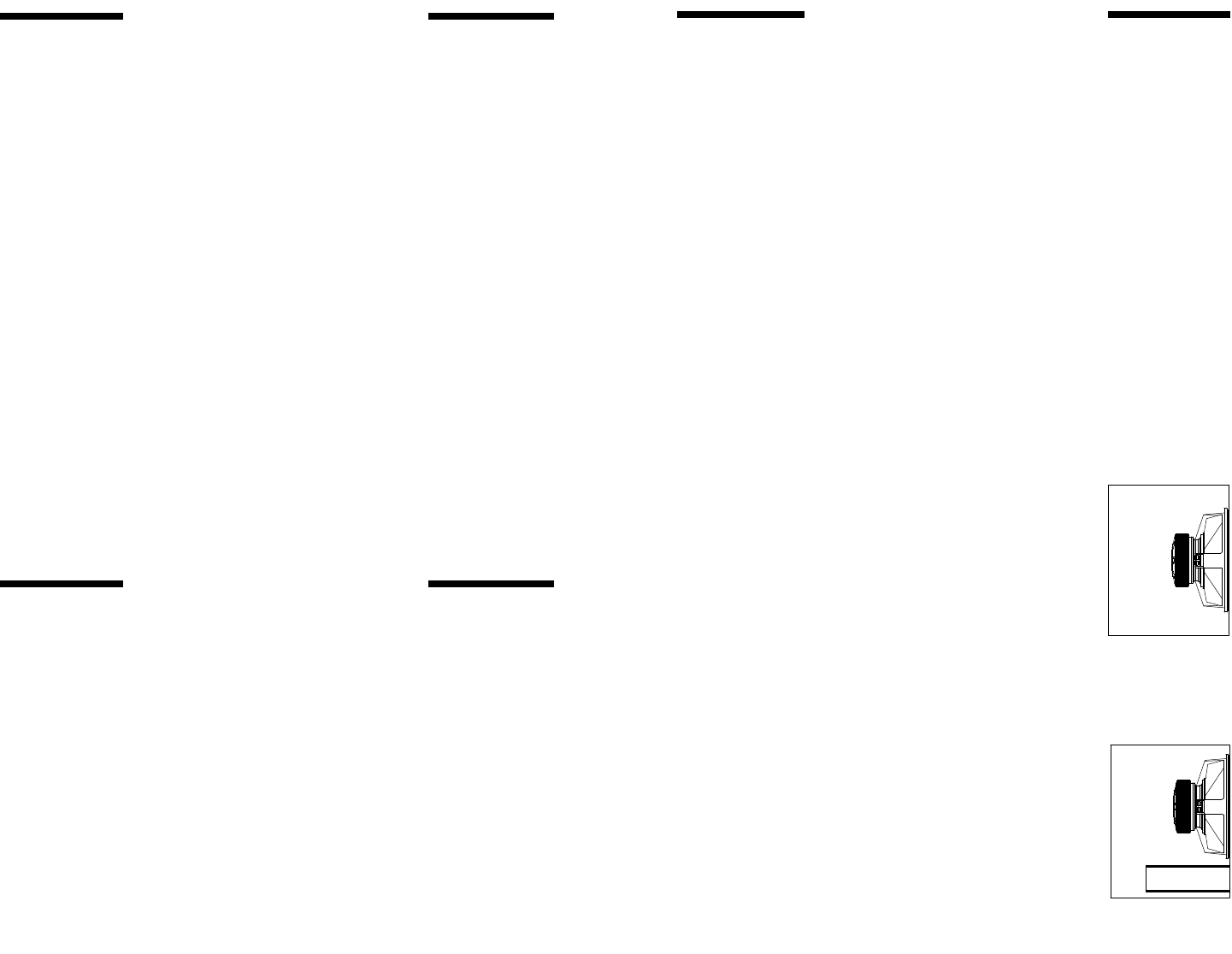
8
BUILDING THE ENCLOSURE
• Determine the dimensions of your enclosure.
• Be certain the box you have designed will fit into the location you have
chosen. Sometimes making a cardboard box with the same outside
dimensions is helpful.
• Use 3/4 inch thick Medium Density Fiberboard (MDF) or High Density
Particleboard. It is preferable to cut the wood with a table saw to ensure
straight, even joints. If a table saw is not available, a circular saw is
acceptable.
• Use a “T” square to verify precise right angle gluing.
• Use a high quality wood glue and air nails or wood screws to assemble the
enclosure. Elmer’s woodworker’s glue and Weldwood work well. To
guarantee an airtight box, seal each inside joint with silicone sealant.
• For Sealed Enclosures, stuff the chamber with 50-75% filling (approximately
1.5 pounds per cubic foot) of fiberglass insulation or Dacron.
• For Vented Enclosures, staple 1 inch thick fiberglass insulation or Dacron to
all walls of the enclosure except the baffle to which the woofer is mounted.
• Use the supplied gasket to seal the woofer in the enclosure and eight(8)
wood screws or T-nuts and bolts. Progressively tighten each of the bolts or
screws to prevent warping the woofer frame.
• Use slide-on connectors to attach speaker wires. Do not solder wires to the
SUGGESTED ENCLOSURES
The following designs include a variety of enclosure sizes and types.
Each design has two frequency response curves; one showing predicted
“In-Car” response, and the other showing “Half-Space Anechoic” (out-of-car)
frequency response. The performance difference between the two curves is a
result of the natural acoustics of an “average” automotive environment. This
“average” transfer function is only an approximation of what you may expect to
see in your car. Every car is different. Each curve was generated using 2.83
Volts across both voice coils in parallel and measured at 1 meter. Also, each
frequency response curve includes a 12 dB/octave low pass at 100 Hz for
sealed and vented enclosures and 200 Hz for bandpass enclosures. The
response curves can help you visualize relative performance differences
between designs. Read through the descriptions given for each enclosure and
select the one that suits your needs.
Remember: all suggested enclosure volumes are Net, and DO NOT include
woofer, port, and bracing displacement!
5
SELECTING AN ENCLOSURE
There are several different enclosure designs for different applications.
The SPL subwoofers work very well in all the following enclosure
designs. It is up to you to select the specific enclosure that will work
the best for your particular application.
Infinite Baffle
Infinite baffle is the simplest type of subwoofer installation. In this type
of installation, the woofer(s) is mounted to a baffle which is then
mounted to either the rear deck or back seat of the vehicle. The best
results are achieved when the trunk area is virtually airtight and
isolated from the passenger compartment.
Sealed Enclosure
Sealed enclosures are relatively simple to build and install, as all that is
required is an airtight box. The larger the sealed enclosure, the more
the performance resembles that of an infinite baffle installation.
Vented Enclosure
Vented enclosures use a sealed enclosure with a vent or port in the box
which is tuned to resonate at a specific frequency.
Pros Cons
• Good low frequency exten-
sion down to the tuning fre-
quency
• High power handling down
to the tuning frequency
• Higher output than sealed
enclosures
• Low power handling
below the tuning fre-
quency
• Almost no output
below the tuning fre-
quency
Pros Cons
• Very good low frequency
extension
• Very good transient re-
sponse
• High power handling
• Medium efficiency
Pros Cons
• Excellent low frequency extension
• Excellent transient response
• Uses almost no trunk space
• Lower power handling
• Low to medium efficiency
Sealed
Vented (V)